半導体ができるまでの工程を公開!チップの作り方や組み立て工程をわかりやすく解説
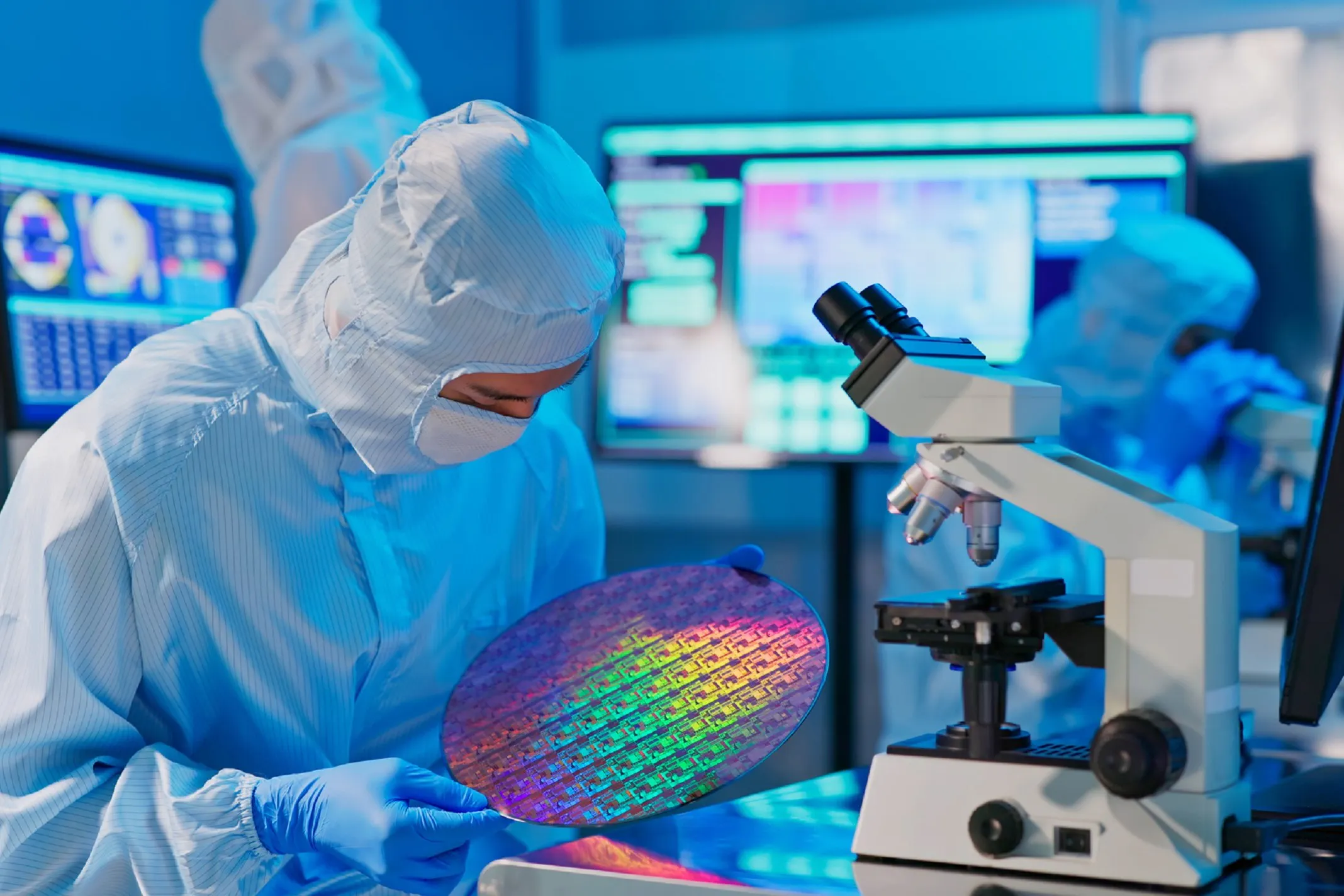
スマートフォンやパソコン、家電から自動車まで、私たちの生活に欠かせないあらゆる製品の中で働いている「半導体」。しかし、半導体のチップができるまでのプロセスは意外と知られていません。
この記事では、半導体製造の全工程や半導体メーカーを解説し、業界の将来性やキャリアの可能性についても紹介します。
半導体とは
半導体とは、電気を通す「導体」と電気を通さない「絶縁体」の中間的な性質を持つ物質です。
物理的な定義では、電気伝導性の良い金属などの「導体」と電気抵抗率の大きい「絶縁体」の中間的な抵抗率を持つ材料やデバイスを指します。機能的には、電気信号の増幅や切り替え、記憶、発光などの機能を実現できる物質であることが特徴です。
主な半導体の材料としてはシリコンが知られています。シリコン原子は4つの価電子を持ち、周囲の4つのシリコン原子と共有結合を形成して結晶構造を作ります。
現代社会を支える基盤技術として、半導体は欠かすことのできない存在です。スマートフォンからコンピュータ、自動車、医療機器に至るまで、日常生活を支える製品に半導体が使われています。
半導体の特徴
半導体の特徴は、温度変化や光の照射、不純物の添加などの条件によって電気の流れを制御できることです。
例えば、半導体に微量の不純物を添加することで、その電気的性質を変化させることができます。リンなどの5価元素を添加すると余分な電子が自由に動き回るN型半導体となり、ホウ素などの3価元素を添加すると電子が不足して正孔と呼ばれる穴が生じるP型半導体となります。
また、半導体は微細化が可能で、小さなチップの中に多くのトランジスタという素子を組み込むことができます。その結果、高機能な電子機器の小型化に貢献しています。
【関連記事】半導体とは?定義や仕組みをわかりやすく解説!3つの役割や日常生活での使用例も紹介
半導体は何に使われる?
半導体はさまざまな製品に使われています。
電子機器 | スマートフォン、パソコン、テレビ、デジタルカメラ、LED照明、家電製品(エアコン、炊飯器など) |
---|---|
自動車 | エンジン制御システム、先進運転支援システム(ADAS)、安全装置 |
医療機器 | CTスキャン、デジタル高画質映像、ヘルスケア機器、歩数計、電子体温計 |
産業機器 | 産業用ロボット、計測機器 |
電子機器分野では、例えばスマートフォンの心臓部として半導体が使用されています。自動車分野では、エンジン制御システムから先進運転支援システムまで、安全性と快適性を高める役割を担っています。医療分野では、CTスキャンやデジタル高画質映像に欠かせず、人々の健康に貢献することが可能です。
社会インフラにおいても、電車の運行管理や交通信号機など日常生活を支える基盤技術として半導体が活躍しています。
【関連記事】身の回りにある半導体製品にはどんなものがある?半導体製造工場で働くには?
半導体ができるまでの工程:半導体チップの作り方
半導体チップが作られる過程は、「設計工程」「前工程(ウェーハ加工)」「後工程(チップ組み立て)」の3つに分けられます。
半導体製造は精密な工程の連続であり、わずかなホコリや異物の混入も製品の動作に影響を与える可能性があります。そのため、製造工程のほとんどはクリーンルームと呼ばれる環境で行われ、作業員もクリーンウェアを着用して異物の混入を防いでいます。
設計工程
設計工程は、半導体チップが持つべき機能や性能を決定し、回路図を作成する段階です。コンピュータを使った精密な計算とシミュレーションにより、半導体チップを設計します。
この工程ではまず、半導体チップ上にどのような回路を配置するかを設計し、シミュレーションを繰り返して効率的なパターンを検討します。用途によって必要な機能が異なるため、設計するパターンも都度異なるものとなります。
次に、フォトマスク作成の段階に移ります。透明なガラス板の表面に、設計した回路パターンを描き出します。これが、シリコンウェーハに回路を転写するための原版(マスタ)となります。
前工程:ウェーハ加工
前工程は、「シリコンウェーハ」という円盤状の基板に実際の電子回路を形成する工程です。
この工程は以下のような順序で進められます。
- インゴットの切断
- ウェーハ作製
- 洗浄
- ウェーハ表面酸化
- 配線パターニング
シリコンインゴットは、シリコンの単結晶の塊です。これをワイヤーソーで薄くスライスし、ウェーハの基盤を作ります。次に切り出されたウェーハを研磨剤と研磨パッドによって鏡のように磨き上げます。
洗浄では、ウェーハ上の不純物や異物を除去します。半導体製造には目に見えないほど微細なゴミの残留も許されないため、この工程も欠かせません。
ウェーハ表面酸化では、ウェーハを高温の酸素にさらすことで表面を酸化させます。この酸化膜は絶縁層となってトランジスタの構成となります。
配線パターニングでは、フォトレジストの塗布、露光、現像、エッチングといった工程を何回も繰り返して、設計された回路パターンをウェーハ上に形成します。
後工程:チップ組み立て
後工程は、前工程で作られたウェーハから個々のチップを切り出し、製品化する工程です。
この工程は以下のような順序で行われます。
- ウェーハテスト
- ウェーハボンディング
- バックグラインド
- ダイシング
- パッケージ
ウェーハテストでは、ウェーハに形成された数百個のチップのひとつひとつに対して、プローブを接触させて電気的に問題がないかを検査します。次のウェーハボンディングでは、シリコンやガラスなどの支持基盤に張り合わせます。
バックグラインドでは、ウェーハの裏面を研削して薄くします。ダイシングでは、ウェーハをダイヤモンド製の「ダイシング・ソー」で切断し、個々のチップに分離させます。
最後のパッケージでは、チップを傷や衝撃から保護するため、樹脂で封入。チップが保護され、電子機器に組み込める状態になります。
【関連記事】半導体の製造工程を大公開!働く際の注意事項についても解説
半導体メーカーとは
半導体メーカーとは、半導体の設計、製造、販売を行う企業のことです。半導体産業が発展していく中で、各企業はそれぞれの強みを活かした事業モデルを構築し、さまざまな形態のメーカーが存在するようになりました。
半導体メーカーはIDM(垂直統合型メーカー)、ファブレス、ファウンドリ、OSAT(後工程受託企業)の4つに分類されます。こうした企業が相互に協力し合うことで、高度な半導体製品の開発と製造が可能になっています。
市場ニーズの変化や技術の進化に応じて、企業形態も変化してきており、例えば以前はIDMだった企業の一部がファブレス化するなど、業界の再編も進んでいます。
IDM(垂直統合型メーカー)
IDM(Integrated Device Manufacturer)は、半導体の設計から製造、販売までを一貫して自社で行うメーカーです。自社で工場(ファブ)を持ち、開発から生産までの全工程を自社内で完結させる垂直統合型のビジネスモデルを採用しています。
IDMの最大の強みは、設計と生産の両方のノウハウをすり合わせて、製品の性能を最大限に高められることです。自社の製造ラインで生産することで、外注コストを削減でき、大量生産する製品はIDMの方が安価になる場合もあります。また、生産管理や品質管理がしやすく、情報漏洩のリスクも低く抑えられます。
しかし、自社で製造設備を保有するため、最先端設備に対する投資が必要となり、市場の変動に対するリスクも大きくなります。それでも、半導体製品の種類によっては、今でもIDM企業のシェアが高い分野もあり、技術力と生産能力を併せ持つIDMは半導体産業において重要な位置を占めています。
ファブレス
ファブレスは、「工場を持たない」という意味の英語に由来するものです。半導体の設計のみを行い、製造は外部企業(ファウンドリやOSAT)に委託します。
自社で生産設備を持たないため、設備投資を抑えられるのがメリットです。また、製品の企画・設計にリソースを集中させることで、市場の変化に対応できる柔軟性があります。ニッチな市場や新興市場にも参入することが可能です。
ファウンドリ
ファウンドリは、他の企業(主にファブレス企業)から委託を受け、半導体の製造を行うメーカーです。主に製造の前工程を請け負います。
ファウンドリの強みは、製造に特化しているため、技術開発や設備投資にリソースを集中できることです。さまざまな企業からまとめて受託することで、自社の生産能力をフル活用し、スケールメリットを活かした大量生産が可能になります。
OSAT(後工程受託企業)
OSAT(Outsourced Semiconductor Assembly and Test)は、主に後工程を行う企業です。ファウンドリが前工程を受託するのに対し、OSATは後工程を受託する役割を担っています。
OSATは、IDMやファブレス企業から半導体チップを受け取り、ダイシング、ワイヤーボンディング、モールディングなどの工程を経て、最終的に製品に組み込める形に仕上げます。
IDMも、自社のキャパシティが不足した場合やリードタイムの短縮が必要な場合に、OSATへ製造を委託することがあります。
【関連記事】半導体業界の年収は高い?企業ランキングや将来性、就職するコツも解説
半導体エンジニアの将来性
半導体エンジニアの将来性は高いと言えます。
IoTやAIの進化に伴い、さまざまな機器やシステムに半導体が搭載されるようになり、市場全体が拡大しています。自動運転車やドローンなどの先端技術が普及するにつれ、より高性能な半導体が求められるようになっています。
こうした市場ニーズの高まりを反映して、半導体エンジニアの採用ニーズも増加しています。電子情報技術産業協会(JEITA)は、今後10年間で主要8社だけで4万人以上の人材がさらに必要になると推測しています。
出典:JEITA半導体部会|国際競争力強化を実現するための半導体戦略 2023年版
また、半導体エンジニアの平均年収は約644万円とされていますが、経験やスキル、勤務する企業によってはさらに高い報酬を得ることができます。
出典:厚生労働省「jobtag」|半導体技術者
半導体業界は技術革新が速く、常に最新技術をキャッチアップする必要があります。そのため、情報の感度が高く、英語力やコミュニケーション能力に長けたエンジニアほど高い評価を受ける傾向にあります。
また「半導体製品製造技能士」や「半導体技術者検定」などの資格を取得することで、キャリアアップにつなげることも可能です。
【関連記事】半導体エンジニアとは?仕事内容や年収、将来性 、有利なスキルを解説
まとめ
半導体は電気を制御する特性を持つ素材で、私たちの生活に欠かせない電子機器の基盤となっています。その製造工程は設計、前工程(ウェーハ加工)、後工程(チップ組み立て)の3段階に分かれます。
半導体業界はIDM、ファブレス、ファウンドリ、OSATなど異なる役割を担う企業で構成され、IoTやAIの普及により市場は今後も拡大が見込まれています。
ワールドインテックのテクノ事業では、こうした成長産業での活躍を目指すエンジニアを支援し、最先端の現場で、スキルと経験を活かせる機会を提供しています。興味のある方はぜひチェックしてみてください。