工場の安全を確保するための「ルール」の重要性|安全を徹底して大きな損失を防ぐ
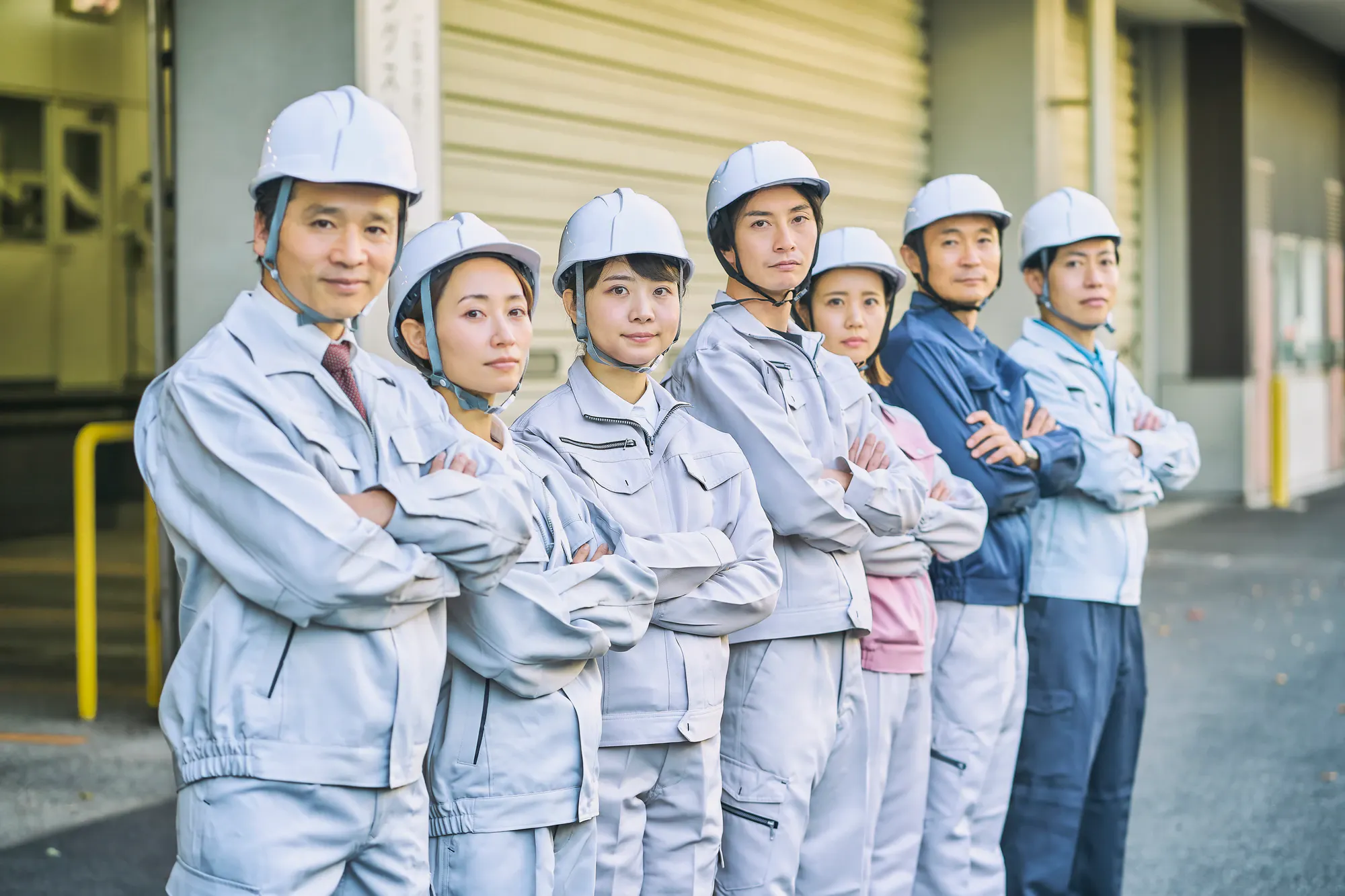
安全対策は工場を稼働させるにあたって必須であり、従業員をけがなく家に帰すことが事業者にとって最低限の責務です。しかし、「機械が作動している工場」「重量物がある工場」「化学物質を取り扱う工場」など、一歩間違えると重大災害につながる工場も多い中で、無災害を目指すことは容易なことではありません。
そこで重要になるのが「工場の安全ルール」です。この記事では、安全ルールの重要性や作り方、作るときのポイントを解説します。
工場における安全ルールの重要性
工場には「保護具の着用」や「一旦停止」などの、安全ルールが存在します。中には作業効率が落ちることや、ひと手間増えるルールもありますが、これらは作業者自身の身体を守るために必要です。
作業中にけがをした場合、本人は痛い思いをすることはもちろん、心や身体に後遺症が出るケースや、最悪の場合死に至る可能性も考えられます。また、けがをした場合は本人だけの問題に限らず、管理者側の問題にもなりえます。その場合、再発防止対策や労災処理の業務が必要になるほか、休業する場合には一緒に働いている作業者の欠員対応をする必要があります。重大災害の場合は、工場の稼働停止によって経営難となり、従業員にも影響が及ぶ可能性も否定できません。
このような事態にならないために設けられているのが「安全ルール」です。安全ルールを適切に定めることで経営側・管理側は守られるとともに、遵守していれば自分自身も守ることにつながるのです。
労働災害の裏には数百もの発生要因がある(ハインリッヒの法則)
一つの重大災害が起こるまでには、300件のヒヤリハットと29件の軽微な事故が隠れていると考えられています。この考え方は、労働災害を考える際に広く用いられる「ハインリッヒの法則」と呼ばれているものです。
ヒヤリハットとは、作業中に危ないと感じて「ヒヤリ」や「ハッと」したことが語源となっており、「事故にはならなかったが危険な状態だった」ということを表現しています。ハインリッヒの法則はヒヤリハットから労働災害につながる法則であるため、労働災害防止の対策としてヒヤリハットの防止は有効的です。
重大災害を起こさないためには、軽微な災害を繰り返し起こさせないことが重要です。さらに、軽微な災害を起こさせないためには、ヒヤリハットを繰り返して起こさせないことが重要となります。
工場で特に注意すべき事故
「何を作っているのか」「どういった設備があるのか」「どういった素材を取り扱っているのか」によって、安全対策するポイントは違ってきます。一般的な工場で注意すべき事故は以下の通りです。
- 転倒事故
- 落下事故
- 巻き込まれ事故
- 感電事故
上記は労働災害につながりやすい項目であるため、特に注意して対策を練ることが求められます。
転倒事故
転倒事故は日常生活の中でも起こり得る事故であるため、足場が不安定な作業があったり、重量物を扱ったりする工場ではなおさら起こりやすくなります。それゆえに、転倒事故は、労働災害の中でも大きな割合を占めています。
転倒事故が発生しやすくなる要因としては、以下が挙げられます。
- 段差がある
- 地面が滑りやすくなっている
- 暗さなどにより床面が見づらい
- 歩行スペースに不要な物が置いてある
これらは「不要な段差はなくす」「滑り止め加工をする」「照明を設置する」「工場内の2Sを行う」などの対策を行うことで転倒のリスクを減少させることが可能です。
転落事故
転落事故は、発生してしまうと命に関わる労働災害の一つです。高所での作業を必要とする業種によっては、起こりやすい事故といえます。転落事故が起こる原因としては、踏み外すなどの人為的なミスが大半です。そのため、作業者が注意することはもちろん、「保護柵の設置」や「ハーネスの着用」といった対策を行いましょう。
巻き込まれ事故
巻き込まれ事故は機械の安全化が進んでいるため、年々減少傾向にあるものの、「操作ミス」「機械のメンテナンス不足」「作業者のスキル不足」といった理由で起こり得る労働災害です。
挟まれや巻き込まれ事故は大けがにつながるおそれがあり、場合によっては死亡災害となる可能性もあります。そのため、従業員だけではなく、会社全体で安全対策を行うことが必要です。
感電事故
感電事故が発生するケースは電気設備を取り扱う企業で起こるイメージですが、自社簡易的な機械の修理や点検を行う際にも発生しやすいので注意が必要です。
災害レベルは電気の規模によって異なります。電気の規模が小さい設備を取り扱う場合は、軽傷で済む可能性があります。一方で電気の規模が大きい設備を取り扱う場合は、重大事故に発展することもあります。感電事故は作業者の知識不足や油断によって事故が発生する可能性が高くなるため、専門家に任せることが大切です。
安全ルールの作り方
工場で労働災害ゼロを目指す場合は、工場に適した独自の安全ルールが必要です。工場によって製造するものや作業工程、使用工具などが異なるため、ルールは工場ごとに定める必要があります。安全ルールを作る際には、やみくもにルールを設定するのではなく、以下のように順序立てて設定しましょう。
- 工場に潜むヒヤリハットを洗い出す
- ヒヤリハットで洗い出したミスなどへの対策を立てる
- 対策をルール化してマニュアルにする
- 全従業員に展開して実施
- 定期的に改善を行う
安全ルールを作る際のそれぞれの手順について詳しく見ていきましょう。
工場に潜むヒヤリハットを洗い出す
初めに工場にどのような危険が潜んでいるのかを知る必要があります。その際に役立つものは、従業員が実際に体験している小さなミスです。そのため、ヒヤリハットを洗い出す際は、従業員に対して定期的にどのようなヒヤリハットがあったかについてヒアリングを行うようにしましょう。
ヒアリングの内容としては、ヒヤリハットを体験した場所や内容、時間帯、どの作業しているときかなどが挙げられます。できるだけ具体的な内容を聞き、正確に洗い出せるようにしましょう。また、ヒヤリハットは安全ルールを作成するときだけでなく、日頃から収集できる仕組みを作っておくことも重要です。
ヒヤリハットで洗い出したミスなどへの対策を立てる
ヒヤリハットの洗い出しができたら、次に洗い出したヒヤリハットに対策を行っていきましょう。対策を出し合う際は、「どのくらいの頻度で発生するのか」「どの程度のレベルの災害につながるのか」といったヒヤリハットの深刻度合いも考慮するようにしましょう。深刻度合いが高い緊急性を要する対策から実施し、深刻度合いの低いものは後回しにするなど、対策を行う順番を決めることも重要です。
対策をルール化してマニュアルにする
立てた対策は、周知やOJTをすることはもちろん、マニュアルに落とし込み「見える化」を行いましょう。
対策をマニュアルにし見える化することで従業員への周知が容易になるほか、新入社員に教えるときに漏れがなくなることや、誰が教えても同じように教えられるといったメリットがあります。マニュアル化することで、安全対策の定着化に役立つのです。
全従業員に展開して実施
全従業員にマニュアルを展開して、早速実践するように指導を行いましょう。マニュアルを作成したものの、作業員が実際に対策を守れていなければ意味はありません。実施するように指導を行うほか、守られていなければ是正指導を行い、定着を図りましょう。展開を行う際は、「聞いていない」という従業員がいないよう、念のためチェック欄を設けて記録に残すことをおすすめします。
定期的に改善を行う
安全ルールを作ったからといって、一度で完璧なものができるわけではありません。作業者に落とし込むときに気づいたことや、実際に作業している人の意見も聞きながら、よりよいものにブラッシュアップしていくことが重要です。さらに、新しい設備の導入や、作業内容の変更を行う場合も、安全ルールを見直す必要があります。
安全ルールの活用効率を高めるポイント
安全ルールは、作業員の安全を守るために存在します。しかし、ルールを守らない作業員がいたり、作業者が本当に望んでいる対策ができていなかったりする場合も多いです。安全ルールの活用効率を高めるためには、以下の三つのポイントを意識して安全対策に取り組むことをおすすめします。
【安全ルールを進める際のポイント】
- 事業者には労働者の安全を確保する義務がある
- 労働者には安全ルールを遵守する義務がある
- 安全委員会等の組織を新たに作成する
事業者には労働者の安全を確保する義務がある
事業者には「利益を確保して従業員に安定した給料を支払う」「水準を満たした品質を顧客に提供する」という義務がありますが、それ以上に大切とされているのが「労働者の安全を確保する義務」です。「安全第一」を掲げているの工事現場を見たことがあるでしょう。工場によっては安全の重要性を強調するために、「安全第一・品質第二」を企業理念として掲げている工場もあるほどです。
「利益を追求しすぎるあまりに安全が疎かになっていた」とならないように、事業者は安全ルールに対する重要性をしっかり理解しておく必要があります。
安全ルールを実施する目的を従業員にしっかりと伝える
事業者が安全ルールを実施する際は、目的を従業員にしっかり伝えることが大切です。そうすることで、一人一人の安全に対する意識が高まり、安全ルールが守られることにつながります。また、事業者が安全の重要性に対して正しく理解していることが、より多くの従業員に伝われば伝わるほど工場全体の安全意識が高まります。
安全ルールを遵守している従業員を正しく評価する
安全ルールの定着化を図るためには、ルールを守っている従業員を適切に評価することも大切です。ただ安全ルールを守らせているだけでは定着が図れない可能性も考えられます。そのため、ルールを遵守しているかについて評価基準を設け、評価によって待遇を良くしたり、表彰したりして従業員に還元していくことが重要です。逆に安全ルールを守れていない人には、是正を行い続けることでおのずとルール定着が図れます。
労働者には安全ルールを遵守する義務がある
いくら立派な安全ルールがあったとしても、労働者がルールを守らなければ意味がありません。安全ルールの一番の目的は、労働者自身の身体を守るためです。ただし、目的はそれだけでなく、企業を存続させていくためや、他の従業員の雇用を確保するためでもあります。
ルールを守らないことで労働災害が起きてしまうと、場合によっては稼働停止になるおそれがあり、企業の売り上げに影響を及ぼしかねません。その影響によって他の従業員の雇用も危ぶまれる可能性もあることから、労働者自身も安全ルールを守る義務があるのです。
安全ルールを正しく理解する
安全ルールを遵守するためには、定められたルールを正しく理解する必要があります。正しく理解できていないと労働者自身に守る意思があっても間違った行動をとってしまう場合があり、災害につながるかもしれません。もし理解できないルールがある場合は、各従業員が質問などをして正しく理解することが重要です。
安全ルールに問題がある場合は素早く指摘する
安全ルールに問題がある場合はすぐに上司へ報告することで、ルールの改善が行えるでしょう。とはいえ、部下が上司に対してルールに対する是正事項を勧告することは難しいです。そのため、上下関係があっても必要なことは申し出られるよう、労働環境を改善する必要があります。また、労働環境を改善することで、従業員が一丸となって安全ルールを遵守するようになることも見込めます。
安全委員会等の組織を新たに作成する
安全ルールを守り労働災害ゼロを目指すには、安全に特化した組織として安全委員会を設置することも有効的です。安全委員会を設置するメリットは以下の通りです。
- 安全についての問題を集約できるので報告なども集まりやすい
- 現場とは別部門で作ることで安全に特化した体制が整えられる
- 委員会を設置することで安全意識の重要性を全従業員に示すことができる
上記のことからも安全委員会などの組織を新たに作成することは、工場の安全を守る上で役立つことが分かります。
まとめ
工場で労働災害が起こるとけがをした本人はもちろん、企業やほかの従業員にも影響を及ぼす可能性があります。そのため、工場では、各従業員が安全ルールを守り、日々無事に作業を終えることが重要視されます。安全ルールを各従業員に遵守させるためには、事業者自体が安全の重要性を適切に理解することが大切です。企業や従業員にとって最も重要であるのは安全であることを理解して、安全ルール作りに取り組んでいきましょう。