製造工場で重要視される「5S」とは|5Sの取り組み方とポイントを押さえて業務効率化を図る
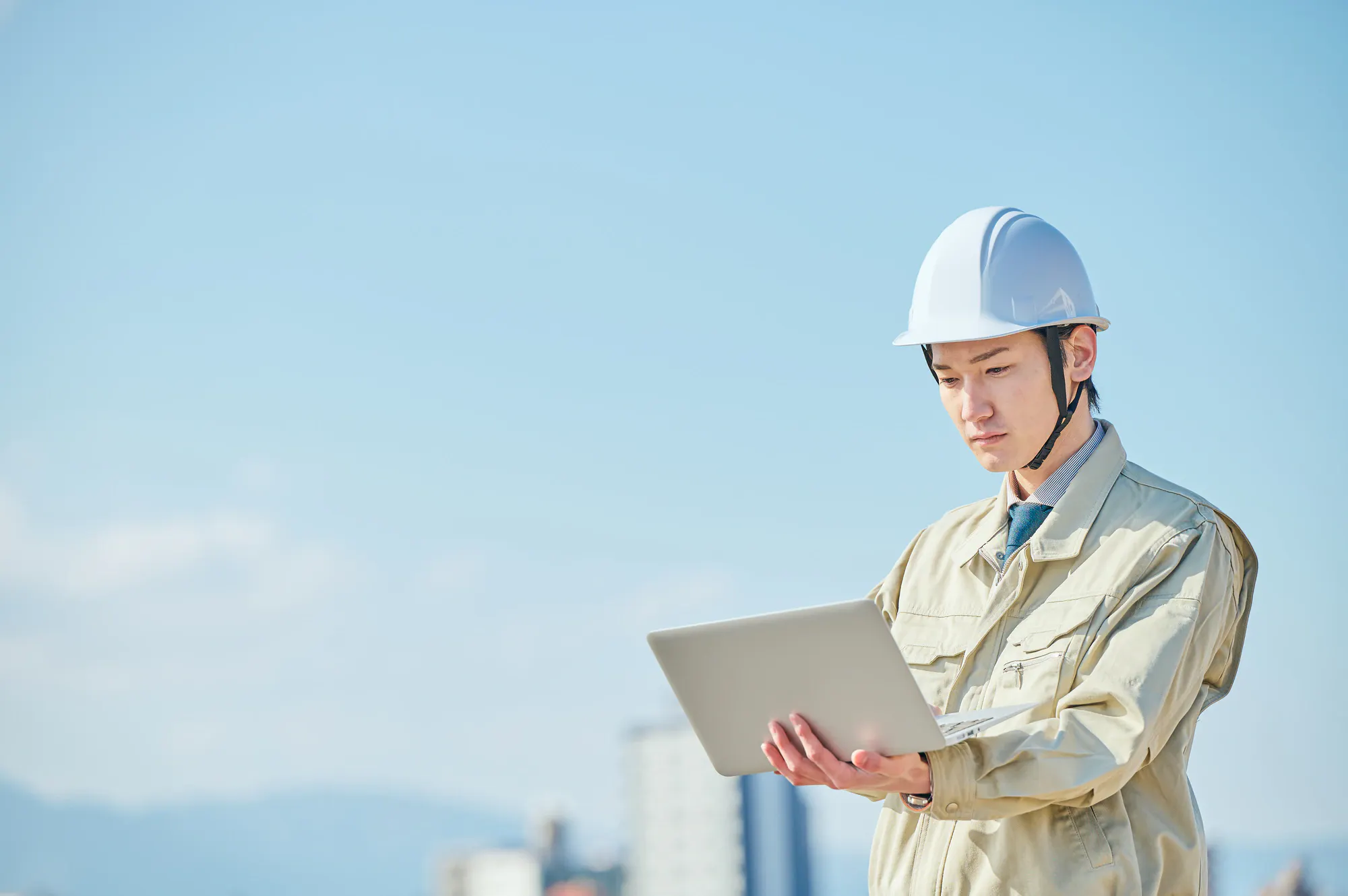
工場における5Sとは、整理・整頓・清掃・清潔・しつけの五つを指します。しかし、業務効率を向上させるべく5Sに取り組みたいと思っても、何をすればよいのか分からない方も多いでしょう。本記事では5Sの各項目で具体的にすべきことと、5Sを徹底することの目的とメリット、実施する際のポイントをお伝えします。すべきことの詳細とその効果を知れば、5Sに取り組みやすくなりますよ。
5Sとは
工場における5Sとは、整理・整頓・清掃・清潔・しつけの五つを指します。これらをローマ字表記すると、Seiri(整理)・Seiton(整頓)・Seisou(清掃)・Seiketsu(清潔)・Shitsuke(しつけ)となり、すべて頭文字がSなので、それを取って5Sと呼んでいます。
工場で5Sを取り入れることで、作業環境を整え、仕事の質を高めたり安全に取り組んだりすることが可能です。整理と整頓、清掃と清潔は似たような言葉ですが、それぞれ目的が違います。以下に簡単に紹介します。
- 整理:工場にある物の要・不要を判断し、不要な物を捨てること。
- 整頓:必要な部品や道具をすぐ取り出せる状態にしておくこと。
- 清掃:日々の作業終了後に、工場や機械を清掃・メンテナンスすること。
- 清潔:整理、整頓、清掃をすることで職場を清潔に保つこと。
- しつけ:上記四つのSを社員全員が常に徹底して行うこと。
こうしてみると、意外とできていなかったと思う項目があるかもしれません。では、なぜ工場において5Sは重要なのでしょうか。次の項目で解説します。
5Sの重要性
工場における5Sとは、事故を防ぐための重要なスローガンです。工場内には大型機械やさまざまな工具など、扱い方を誤ると事故につながるものが数多くあります。それらを誰もが、いつでも安全に使用するためには5Sの実施が欠かせません。
さらに、5Sの実施は作業効率を上げることにもつながります。例えば、工場内で部品や道具、指示書などをいつも探していませんか。その場合、整理・整頓の二つのSを実践すれば解決でき、それらを探す時間がなくなるので業務効率も上がるのです。また、毎日清掃をして清潔な環境を保てれば、企業のイメージアップにも従業員のモチベーションアップにもつながります。きれいな場所で働くほうが心にゆとりをもって仕事ができ、結果として事故を防ぐことにもなるのです。
5Sの目的
先ほど工場で5Sを実施すると業務効率が上がるとお伝えしましたが、それを含め5Sを行う目的は以下の四つです。
【5Sの目的】
- 安全面の向上
- 業務効率化
- 従業員(組織)同士の連携を円滑にする
- 職場環境の良質化
最終的にはこれら四つによって、会社や従業員、株主に利益が還元されることが一番の目的です。それぞれ詳細を確認し、意味のある5Sを実施していきましょう。
安全面の向上
5Sの徹底によって安全性が向上し、事故の予防につながります。整理・整頓が行われれば不用品で工場内があふれかえることもなく、通路に物が置かれて通れないということもなくなります。他にも毎回清掃を行うことで機械のメンテナンスもできるので、いち早く劣化や不具合に気づくことができ、事故を防げるでしょう。
業務効率化
5Sの中でも「整理」「整頓」は、特に業務効率を向上させる効果があります。まず要る物・要らない物に分けて整理をし、それから保管場所などを決めて整頓をし、どこに何が、いくつあるのかを明確にしましょう。
中には今は使わないものの、この先使う可能性があるものも出てくると思います。その場合は、物品に合わせて保管期間と保管場所を決めておきます。例えば資材は1カ月、機械は3カ月といった具合です。いつからいつまで保管するのかを紙に書いて貼っておけば、さらに整理がしやすくなるでしょう。
数や場所の把握によって従業員がスピード感をもって作業できるようになるので、生産性を高めることにつながります。
従業員(組織)同士の連携を円滑にする
5Sを通じて仕事の取り組み方やり方や物の配置などのルールを共有できるため、従業員同士の連携が円滑になります。
工場内では個人間や部門間で認識がずれると連携がしにくくなり、それがミスや事故の原因となってしまいます。5Sを徹底して守ることで、どこに何を置いてあるのか、処分方法や保管場所はどうするかなど共通認識が生まれるので、連携しやすくなるでしょう。
職場環境の良質化
5Sを実施すれば、不要な物が減り、工場内が清潔に保たれます。それにより、きれいで仕事がしやすい環境になるのです。
職場が汚れていたり、悪臭がしたりすると従業員のストレスにつながります。小さなストレスかもしれませんが、それが積み重なれば体調を崩す引き金となったり、イライラしながら働くことになったりするでしょう。イライラすると余裕がなくなり、丁寧な作業もできず製品の質を落としかねません。
そうならないように職場環境を整えることは、従業員が気持ちよく働けることにも関わり、それが最終的に生産性の向上や会社の収益にも結び付きます。
5Sによって得られるメリット
5Sを行うことによって得られるメリットには、以下の五つがあります。
【5Sによって得られるメリット】
- 企業イメージがアップ
- 品質・コスト・納期の改善
- 保全業務との連携が図れる
- 人材育成につながる(自走力の強化)
- 従業員のモチベーションの維持
目的と重なる部分もありますが、改めてメリットを確認し、工場内で従業員が納得して5Sに取り組めるようにしていきましょう。
企業イメージがアップ
5Sの徹底により、企業のイメージアップにつながります。工場の清潔さにより第一印象が良くなるのは、想像に難くないでしょう。
また製造業において5Sはできて当たり前ですが、それを当たり前に実施していることは顧客の評価に結び付きます。加えて5Sの徹底は、工場の安全性が確保されており質の高い製品を作ることができるという保証にもなるでしょう。
品質・コスト・納期の改善
5Sは作業環境を整えるだけではなく、QCD(Quality:品質、Cost:コスト、Delivery:納期)の改善にもつながります。なぜなら作業環境を整えることで、従業員の集中力や判断力なども向上するからです。それらが低い状態ではまともな製品は作れず、ミスや事故が発生し、納期に間に合わなくなるリスクすらあります。
しかし整理整頓された清潔な職場なら集中して無駄のない作業ができるため、納期に余裕をもって高品質な製品が作れるようになるでしょう。さらに、不用品が整理されているので、余分な部品や道具を発注する必要もなくなり、コストの削減も可能です。
保全業務との連携が図れる
5Sの中でも「清掃」は日々の機械の保全業務等と連携を図ることが可能です。
例えば、機械を清掃作業にメンテナンス項目を取り入れることで、機械の異常を早期に発見しやすくなります。異常のサインに気づければ、生産のロスを防げるでしょう。
人材育成につながる(自走力の強化)
工場全体で5Sに取り組むことは、人材育成にもつながります。企業における人材育成とは、会社に貢献する人を育てることです。従業員が整理・整頓や清掃を意識的に行い、習慣化することで業務効率はアップします。業務効率が向上すれば、生産性も上がり、企業に利益をもたらすことになるでしょう。さらに、5Sは従業員同士が連携して行うので、自然と人材育成の輪が広がっていくのです。
従業員のモチベーションの維持
整理・整頓、清掃が行き届いた職場で働くことは、従業員のストレスを減らし仕事へのモチベーションを維持できます。仮に、5Sが行われず、ゴミや不用品があふれている工場で働いているところを想像してみてください。そこで働きたくないのはもちろん、出勤もしたくありません。荒れた場所での仕事は、ストレスが募る一方です。しかし、5Sで工場がきれいな状態であれば、前向きに出勤できて、気持ちよく働くことができるでしょう。
5Sに取り組む方法
5Sの目的やメリットを意識した上で、実際に5Sに取り組む方法を項目ごとに紹介します。漠然と5Sをやるのではなく、一つ一つの項目の意味と、具体的にすることを理解した上で実践すれば、より早く効果を実感できます。
整理
必要な物と不要な物の基準を明確にして、不要な物は期限を決めて処分しましょう。例えば、この先1カ月の生産で要るのか要らないのかを判断し、要らない物には保管期限を明記した紙を貼っておきます。紙を貼っておくのは、従業員全員が要らないと判断された物だと理解できるからです。期限が来ても必要がなければ、処分しましょう。
注意することは、ゴミを捨てたり、物を置きなおしたりするだけのただの掃除では一時的な効果しか表れないことです。その場しのぎではなく、継続して整理が行える仕組みを試行錯誤しながら作っていきましょう。
整頓
整理をした後、取り出しやすく戻しやすい場所に必要な物の定位置を決めて、従業員で共有することです。共有するためには口頭で伝えるだけではなく、一覧表を張り出しておいたり、看板を付けたりするとよいでしょう。仮に置き場を覚えられずとも、それを確認すれば誰もが、どこに何があるかを確認状態にすることが肝要です。
また、置き場が未定の物を保管する仮置き場を設けると、通路を塞いだり必要な物と混ざったりすることもないので、ミスや事故を防ぐことができます。
清掃
清掃は日ごろの清掃を丁寧に行い、気持ちのよい仕事環境作りをすることです。また、同時に機械や道具のメンテナンスも行います。整理・整頓ができていると工場内はきれいに見えるので、清掃の重要さが感じにくいかもしれません。しかし、メンテナンスを行うことで点検として位置付ければ、清掃の意味もはっきりとし、従業員も意欲的に取り組めるようになります。
日々のこまめな点検により、機械や作業場の異変にすぐ気づくことができるため、重大なミスや事故を防ぐことが可能です。さらに、きれいな職場で働けることは、従業員のモチベーションの維持にもつながるでしょう。
清潔
整理・整頓・清掃ができている状態を維持することです。つまり、汚れてからきれいにするのではなく、常に作業しやすい環境になるように日々5Sを心がける姿勢が「清潔」の根幹です。
整頓の段階で決めた所定の位置に道具があるか、清掃とともにメンテナンスはしっかり行われているかなどを意識し、清潔な状態を保ちましょう。
しつけ
上記の四つのSを守り実行するために共通のルールを定め、従業員全員が習慣化できるようにすることです。
四つのSは、一度実施しただけでは意味がありません。たとえ新人が入ってきても、同じ会社の他部署に移っても全員が確実に実行できることが重要です。誰か一人でも怠けてしまうと、怠けの輪が広がり元に戻ってしまいます。それを防ぐために5S徹底のリーダーを決め、実施できていない人を見つけたらその場で注意し、習慣化の手助けをするとよいでしょう。
5Sの取り組みにおける質を向上させるポイント
5Sの質を向上させ、効果的に取り組めるようにするためには、下記の三つのポイントが重要です。
【5Sの取り組みにおける質を向上させるポイント】
- 全社員が取り組める仕組みを考える
- 5Sは常に改善する意識で取り組む
- 社員の5Sに対する理解を深める
実りのある5Sを実施するためにも、個々の項目をしっかりと確認しておきましょう。
全社員が取り組める仕組みを考える
5Sは従業員全員で取り組まないと意味がありません。一人でもやらないと「やらなくてもよい」という意識が広がってしまうからです。その連鎖はあっという間に広がり、元の木阿弥です。整理・整頓されたはずの道具や機械はぐちゃぐちゃになり、再びどこに何があるか分からない状態になってしまうでしょう。それを防ぐためにも、ベテラン社員も若手社員も5Sの意義を理解して、前向きに取り組めるような仕組みを考えましょう。
まずは、5Sのそれぞれの項目で、何をすべきか明確にし、共有します。その際に、誰もが無理なくできる内容にすることで、5S実施のハードルを下げることができます。そして、現場の従業員だけではなく経営者が率先して実施する姿勢を見せることが重要です。経営者が5Sの推進者となり、従業員のお手本となりましょう。
5Sは常に改善する意識で取り組む
習慣化された5Sは常に改善する意識で取り組みましょう。習慣化してしまうと、なぜやっているのかが不明瞭になり、やらなくてもよいのでは?と、5S不徹底のきっかけになってしまうからです。
それぞれの項目で効果の検証をし、改善をしていくことでより5Sの効果を発揮できます。効果の検証を行うためにも、まずは目的を明確にしましょう。例えば「整頓」の項目は、すぐに道具が使えるようにすることが目的の一つです。道具の位置を定めた後、毎月1回きちんと所定の位置に道具が規定数収められているかチェックするだけでも、効果の検証ができます。道具が規定数揃っていなければ5Sを徹底できていないことになり、改善の余地ありと判断できるでしょう。
社員の5Sに対する理解を深める
5Sの意味や目的、メリットなどについて社員全員が理解を深めるチャンスを定期的に設けることが重要です。それにより、よりよい職場環境を持続させることができます。
最初のうちはルールを守らなければと従う人も多いかもしれませんが、だんだんと面倒になってくるかもしれません。また、ベテラン社員の中には「掃除なんて新人がやればいい」と感じる人もいるでしょう。しかし、5Sは従業員全員で取り組まなければ効果を発揮しません。一部の人だけがやるのではなく、全員が納得して取り組めるようにするためにも、5Sについて理解を深める機会を定期的に設けましょう。自社でするのが難しければ、社員研修の専門家に頼むという方法もあります。
まとめ
「整理」「整頓」「清掃」「清潔」「しつけ」の頭文字を取った5Sについて、その目的やメリット、導入方法を紹介しました。改めて、5Sの各項目について簡単にまとめておきます。
- 整理:工場にある物の要・不要を判断し、不要な物を捨てること。
- 整頓:必要な部品や道具をすぐ取り出せる状態にしておくこと。
- 清掃:日々の作業終了後に、工場や機械を清掃・メンテナンスすること。
- 清潔:整理、整頓、清掃をすることで職場を清潔に保つこと。
- しつけ:上記四つのSを社員全員が常に徹底して行うこと。
工場における5S導入の目的は、安全性や生産性の向上だけではなく、従業員同士の連携を強め、職場環境を清潔に保つことです。また、5Sを実施すれば顧客からの企業イメージがアップするだけではなく、品質・コスト・納期の改善や保全作業との連携が可能になり、さらに人材育成にもつながります。
ただし、5Sは従業員一丸となって取り組むことがなによりも重要です。そのためには経営者が率先して5Sを実施し、従業員が5Sの目的やメリットを理解できるよう見える化したり、誰でもできるよう取り組み内容を簡素にしたりするなどの工夫が必要です。5Sを定着させ、業務効率アップを目指していきましょう。